Reinventing Quality Linen Services Owner Dicky Smith Expands, Streamlines & Improves Plant for Hefty Gains
September 2018
When Dicky Smith acquired Quality Linen Services (Quality Linen) in 2014, he did so with a mission – to improve efficiency, grow production and achieve the critical mass necessary to produce 100 laundry pounds per operator hour (PPOH). Since then, the industrial laundry, located in Salisbury, Md., has upped production from 1.5 to 12 million pounds per year. But, these results didn’t come without shaking things up.
Due Diligence
Together with Chief Engineer Dan Plaskon and Operations Manager Doug Colonna, Smith analyzed every sector of the business for efficiency, including pickup, sorting, washing, ironing, packaging and delivery. “It was pretty easy to see where the major bottlenecks were occurring,” said Smith. “We set out to improve 150 percent across the board.”
As the ship was tightened and processes streamlined, Smith’s gaze fell on Quality Linen’s production equipment. In order to grow and achieve needed production, he required additional equipment and automation. To make room, he tripled the plant’s square footage from 10,000 to 30,000.
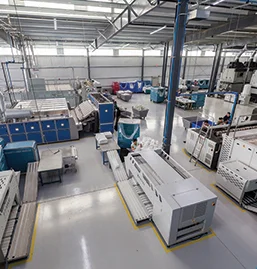
“Our goal was to be a healthcare laundry provider,” he said. “We designed the plant and our equipment makeup for healthcare.” Yet, Quality Linen does it all. Located 30 minutes from Ocean City, a resort town that bustles during the summer, Quality Linen also processes overflow hospitality laundry for hotels and resorts. The plant is equipped to be flexible to serve all customers efficiently.
Equipment Additions/Automation
To get it properly outfitted, Smith worked closely with a team of engineers and specialists at Girbau Industrial (GI). He was familiar with GI equipment because the plant already utilized a seven-module GI Eco-Tunnel, an ironing line and an open-pocket wash line with two Continental Girbau (Continental) 125-pound Pro-Series II Dryers, and E-Series 90- and 55-pound capacity washers.
To reach optimal PPOH, the GI team recommended the addition of a second tunnel system, two ironing lines, and additional open-pocket 255-pound capacity E-Series Washers. In 2016, Quality Linen completed those additions. As part of the startup process, GI engineers trained staff on routine maintenance and operational procedures.
“The GI team is world class,” said Smith. “They took our input and gave us the support we needed. They brought in great people to help and invested a lot in training our staff on preventative maintenance, operation and troubleshooting. Today we are self-sustaining and can do it all in-house.”
“It’s unique to have mixed-use plant in the industry,” said Seth Willer, GI national sales manager. “Their location is kind of remote and Dicky does a great job of capturing his market and serving a bunch of different industries. He does it all and does it well.”
A Second Tunnel TBS-50 Continuous Washing System
Like the first system, the new 12-module TBS-50 Eco-Tunnel operates with water reclamation, water filtration and drain-water heat recovery systems for maximum efficiency. Complemented by loading conveyors, presses, dual-cake delivery shuttles and 10 ST-100 Dryers, the tunnels process 5,000 total laundry pounds per hour – a 300 percent increase in production. Programmable by module, the tunnels use less than a gallon of water per laundry pound and complete 110-pound loads every two minutes.
They also require very little labor, according to Smith. One operator selects a customer number and program on the central computer screen and loads the tunnel conveyor. The tunnels automatically track, wash and dry each 110-pound load. While sheets are quickly separated in the dryer and fed into an ironing line while still damp, towels are completely dried and run through the laundry’s automated folding and sorting systems.
Thanks to the tunnel addition, Smith enjoys peace of mind. If one tunnel fails, the other can operate at night to keep production on track. Although he could run two shifts, he prefers to keep it simple for now.
“We can wash north of 5,000 pounds per hour,” said Smith. “Now the question becomes how many shifts? We process 12 million pounds in a single, 9-hour shift. If we ran two full shifts, we’d process 22 million. But, we don’t need to be that busy. We are a redundant shop in terms of the facility and equipment. But if something were to happen, we could use the other 15 hours a day to correct it. If one tunnel goes down, we can use the other at night to make up for it.”
GI Ironing Lines
On the ironing side, Quality Linen has three GI ironing lines and each features a chest ironer and corresponding folder/stacker. “We iron sheets, scrubs, pillowcases and bath blankets,” said Smith. “Adding automation reduced our labor costs and improved the quality of our final product.” The GI ironing lines also process hospitality linens during the summer months, according to Smith.
Gas operated and 93 percent efficient, the GI ironers automatically adapt cylinder speed according to linen type and moisture content – eliminating the need to pre-dry items. Rather, items are dried as they pass through the ironer, which boosts production and lowers natural gas usage, according to Smith. Programmable to meet specific needs, the GI ironing lines require three operators each – two to feed and one to catch – and operate at speeds up to 164 feet per minute. At the front of one of the ironing lines, a DRF multi-station spreader feeder automatically straightens items and feeds them into the ironer. The feeder addition further boosts processing speeds and ironing quality for amped production and a superior final product, Smith said. Finally, a fourth ironing line, which is dedicated to healthcare goods, consists of a Chicago feeder, ironer and folder.
On the dry goods side, Quality Linen relies on two Foltex folders to quickly fold terry, thermals and gowns out of the dryer. “Automation is important because this is a labor-intensive business,” said Smith. “It’s much more accurate and efficient to automatically fold items using machinery over hand folding.”
Open-Pocket Wash Line
Finally, a hard-working open-pocket wash line tackles niche laundry and heavily soiled items. In 2016 – with the plant’s expansion – it added 620 pounds of capacity to that line. Comprised of E-Series soft-mount washers and complementing dryers, the open-pocket wash line features one 55-, one 90- and three 255-pound capacity washers. “These are programmed for more mechanical action and longer cycles to clean heavily soiled items like napkins,” said Smith. The line is reserved for about 20 percent of Quality Linen’s production needs, which include hospitality and food and beverage laundry. The soft-mount washers reach high extract speeds for moisture removal and quicker dry times – once again giving production a boost.
Cleanovation™ Laundry Care System
To ensure the best-possible clean, Smith uses Cleanovation Laundry Care System, a system that’s new to North America. “We just switched our wash formula to a caustic free, completely natural formula that kills microbes and provides for cleaner loads,” said Smith. “Linens last at least twice as long and it’s environmentally friendly. The city measures our oxygen and phosphate levels. We have zero. We also get tested for microbe-colony forming units. If you score a 20 or less you pass. We typically score a zero.”
Strengthening Labor
At a time when the commercial laundry industry struggles to find quality labor, Smith doesn’t. “We start employees at $10.25 per hour and don’t have difficulties finding help,” he said. “No one makes minimum wage; our working conditions are very nice and we don’t experience much turnover.”
Today, Quality Linen serves a mixed market with a strengthened employee base, considerably more equipment automation, improved energy-efficiency and streamlined operational practices.
“Machinery, efficiency and production fall right into my wheelhouse,” said Smith, who grew up on a farm and has led a number of companies throughout his career. Legally deaf since 1992, Smith regained his hearing after cochlear implant surgery a year ago. It’s no wonder he’s sympathetic toward disabled workers. Since he acquired the struggling Quality Linen four years ago, he’s gone from five employees to 86. Several of them are disabled. “One of my best employees is deaf and I have two with epilepsy and several with autism,” he said. “Some folks can’t do it physically, but if they can achieve 80 percent efficiency, that’s good enough for me.”
In the end, Smith’s goal is to provide a quality product and service to his community, along with happy employees. “All decisions today are made with an eye on five years out,” said Smith.
Thus far, he’s achieved his goals. Quality Linen’s production has skyrocketed, but not at the expense of employees or customers. Quality, redundancy and efficiency are better than ever.
Find out more about Quality Linen at www.qualitylinenservice.com. Discover more about Girbau Industrial at www.girbauindustrial.com, or call 800-256-1073.