San Diego Laundromat Owner Develops Commercial Laundry from Scratch: Phase One Complete
March 2019 | Download Testimonial
Vended laundry owner gone commercial, Brian Voytovich recently completed the first phase of his newest endeavor – the development of 36,000-square-foot Revolve – a new commercial laundry in San Diego. Featuring Girbau Industrial equipment and catering to the hospitality industry, the built-from-scratch operation churns out 35-45,000 pounds of customer owned goods (COG) per day. And, it’s just a year in.
During phase two and three, a tunnel system and third ironing line will be added in order to reach a potential throughput of 100,000 laundry pounds per day. All of this to serve a need.
It Started with an Inkling
Voytovich morphed from vended laundry owner to commercial laundry owner as a result an inkling, which spurred him to action, which unveiled a market need. Previously, his laundromats frequently processed overflow hotel laundry. It seemed there was ample hospitality laundry to go around …
Voytovich explored his idea. “I walked into 20 hotels and did a sample study on who outsourced and if they liked the companies they used,” he said. “I discovered 13 of the 20 outsourced and all were dissatisfied with the service and/or quality received.”
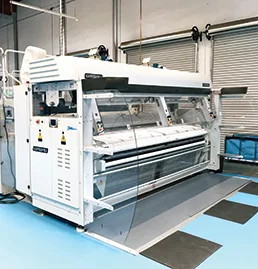
Planning & Development
All in, he sold his laundromats and secured a facility 100 yards from the Mexican Border. During the 14-month development process, Voytovich worked closely with Girbau Industrial (GI) National Sales Manager Seth Willer, who he credits with designing the laundry’s layout and equipment mix. “Seth developed profit-and-loss and forecasting spread sheets, the laundry layout and flow, and determined our expectations for laundry poundage,” said Voytovich. “He was a huge contributor.”
“Brian basically started the laundry from scratch, which doesn’t happen too often,” said Willer. “He came to us asking what he needed for equipment. He gave us a space and we designed the laundry to be flexible in order to handle a variety of items and customer types. The idea was to start small and bring in additional automation in later phases.”
“At the time, I didn’t even know what ironers or tunnels were,” admitted Voytovich. “I was familiar with GI through experience with Continental laundry equipment on the vended side. The machines are well built with high-extract speeds for more production and longer linen life.”
Eco-Friendly, Flexible Equipment Mix
Operational in January 2018, Revolve is equipped with a combination of equipment and systems that make it highly efficient, flexible and eco-friendly The wash line is comprised of six 255- and six 130-pound, high-speed GI washers and matching moisture sensing and reversing dryers.
Voytovich chose the washers for their programmability, soft-mount design and high extract speeds. The soft-mount design simplified installation since no bolts or grout were required. And, because the washers generate extract speeds up to 387 G-force, they remove more water per load, cut resulting dry time and lower gas consumption.
They’re also highly flexible in terms of programmability – allowing Revolve to properly clean a wide variety of items and soil levels, according to Voytovich. “Every hotel is different, so we fine tune our wash programs to fit them,” he said.
Finally, the washers seamlessly interface with the plant’s Voltea capacitive deionization system. “Eighty percent of the water is recycled in the laundry and it is twice as clean as tap water,” said Voytovich. “We were the first laundry in the area permitted for water recycling and are among the greenest laundries in North America.”
On the dryer side, a thermal heat recapture system works to minimize gas usage, while moisture sensing eliminates over-drying and fabric damage. Altogether, 45 percent of the thermal exhaust used by Revolve is recycled and nearly 40 percent of its electricity is generated via solar power.
Ironing & Folding Automation
By adding machine automation, Revolve also ensures high-quality results, greater production and reduced labor hours. To expedite the folding process, dried towels and blankets are fed through one of two GI FT-Maxi towel folders, where they are automatically classified, folded and stacked at a rate of 900 pieces per hour.
Meanwhile, damp sheets, duvets, table linens and pillowcases go straight from the open-pocket washers through a Chicago picker and sorter into one of two finishing lines. Items that demand a high-quality finish, like duvets and table linens, run through the GI finishing line; whereas sheets are typically processed by a Jensen 3-roll ironer with corner-less feeder.
The GI ironing line includes a DRF 3-station spreader/feeder, which automatically straightens and feeds linens into a corresponding PC-120 natural gas, heated-chest ironer. The feeder features a vacuum box and feeding table for best-quality feeding and operates with up to three operators. The GI PC-120 Ironer has two 48-inch diameter rolls, operates at up to 93 percent efficiency and processes items at speeds of up to 164 ft./min.
Finally, flat goods automatically move from the ironer through an FRB Flatwork Folder. Offering an advanced control and multi-program operation, the folder performs one or two primary folds on one, two or four lanes. This results in consistent stacks that are easy to transport and inventory, according to Voytovich.
Cloud-based Management System
Pulling it all together – from inventory tracking to customer management – is Revolve’s LinenTech Commercial Laundry Management Software. “We love it and so do our customers,” said Voytovich. It tracks items by customer as they come in the door, move through the laundry and are delivered back to the customer. Customers can log into our Web portal to view and pay invoices, view and modify orders, and access the status of orders processing and shipping,” he said.
All laundry systems are high tech by design – ensuring customer goods are never intermingled and inventory is accounted for. Delivery drivers use tablets and wireless scanners to track goods by customer. Laundry is placed in color-coded carts by customer and weighed. A computer terminal hooked up to the scale automatically uploads the data into the LinenTech cloud, where it is tracked through the wash and delivery processes.
Thus far, Revolve employs 108 team members while running 2.5 8-hour production shifts. “This month we hit a million pounds processed,” said Voytovich. Come fall, throughput is expected to explode with the completion of phase two and the addition of a 13-module tunnel washer. “Our team is fantastic and we are happy with our progress so far,” he said. “We look forward to serving the Southern California market for many years to come.”
Discover more about Revolve Laundry at revolvelaundry.com. To find out more about Girbau Industrial, www.girbauindustrial.com, or call 800-256-1073.