Home to America’s largest indoor waterpark, the 997-room Kalahari Resort (Kalahari), in Round Rock, Texas, offers families an all-underone- roof getaway with activities for all ages. Amenities include a 223,000-square-foot indoor waterpark, 80,000-square-foot Tom Foolery’s Adventure Park, four onsite signature restaurants and a full-service luxury spa. Behind the scenes, an on-premise laundry quickly processes 20,000 pounds of towels, comforters, blankets, sheets and pillowcases daily.
Designed for Maxed Throughput, Quality and Labor Efficiency
The laundry, an 18-month project from concept to completion, is outfitted with a mix of Girbau Industrial (GI) washer-extractors, drying tumblers and ironing systems engineered for productivity, efficiency and quality, according to Assistant General Manager Karolyn Doro. “We have a great partnership and relationship with the GI team,” she said. “They understood our goal was to build a laundry providing the ultimate productivity and highest quality appearance standards.”
Like the other three Kalahari properties — located in Poconos Mountains, Penn., Wisconsin Dells, Wis., and Sandusky, Ohio — Round Rock invested in top-quality linens for an exceptional guest experience. Moreover, with its opening in November 2020, the Kalahari, Round Rock, began triple sheeting all guest beds. “Our goal is to provide the best experience and highest quality rooms to our guests, which includes crisp, perfectly made beds,” said Doro. “This is only possible with perfectly pressed sheets.”
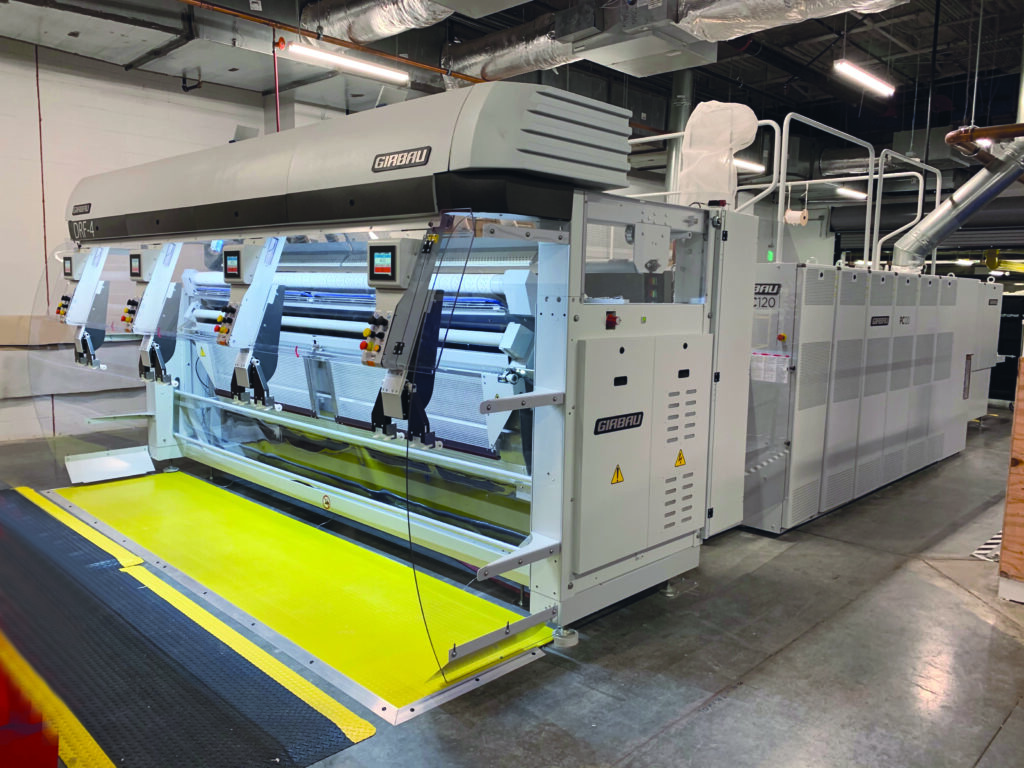
Together with architects and Kalahari executives, GI’s National Sales Manager Brennan Pollnow designed the laundry to achieve targeted production, labor and quality goals, top among them, the ability to quickly wash and flawlessly iron and fold flatwork bed linens.
The Laundry Process Begins with Sorting & Washing
The laundry process starts with help from a Speed Check soil sort conveyor, which allows associates to sort laundry continuously at waist level without stooping. Once sorted, laundry is loaded into one of nine GI soft-mount washers, including four 255-, three 130- and two 60-pound capacity machines. The washers are programmed with multiple cycles for perfectly cleaning resort laundry, according to Doro. Each program controls water levels, cycle time, water temperatures by degree, automatic chemical injection, number of baths and rinses, extract speeds, mechanical action, and more. Additionally, the four largest washers feature two-way tilting for easy loading and unloading. Associates simply load, enter a program number and press start.
Impact of Soft-Mount Washers on Productivity & Installation
Engineered for maximizing throughput, the soft-mount washers reach and sustain high extract speeds up to 386 G-force for significantly more moisture removal than traditional hard-mount washers, which produce speeds between 100-200 G-force. As a result, according to Pollnow, drying time is reduced by up to 30 percent — boosting laundry throughput while reducing labor hours. “This also means dryers operate less frequently, which reduces natural gas consumption and associated utility costs,” he said.

Vacuum-Loading GI Dryers
Once washed, blankets and towels are dried in a GI ST1300 vacuum-feed dryer, whereas flatwork sheets and pillowcases bypass the dryer, and instead, are fed directly into the Kalahari’s ironing line while damp.
The dryers offer vacuum feeding and feature 130 pounds of drying capacity. “Ergonomic for operators, they complete a load of thick terry towels in less than 18 minutes using infrared moisture sensing,” said Pollnow. “The moisture sensing prevents over-drying and extends linen life, which is critical because linen inventory is very expensive.”
Altogether, it takes less than 60 minutes to wash and dry a 130-pound load of terry towels, according to Doro. Once dry, towels automatically unload into the carts below and are sent through one of the property’s three Foltex towel folders. Meanwhile, blankets and comforters are hand-folded.
GI High-Speed Ironing Line
On the ironing side, flatwork sheets and pillowcases are quickly fed, dried, ironed, folded and stacked by a GI ironing system with two to four operators. The system seamlessly integrates three machines in tandem, including a DRF 3-station auto-clip feeder, a PC120 2-roll thermal fluid ironer and an FRB Folder with side stacker. The high-speed ironing line is capable of processing up to 750 sheets per hour, according to Pollnow, allowing the resort to triple-sheet guest beds without adding production time or labor hours.
The ironing process begins with operators attaching the corners of sheets to clips on the DRF Feeder. The DRF Feeder, which is quickly convertible to handle king sheets in one lane or pillowcases in four lanes, features a vacuum table that holds and smooths items as they move toward the ironer. Simultaneously, a vacuum box and spreading brushes pull items tight for high-quality ironing results. As items enter and pass through the ironer, they are automatically dried and ironed. Finally, items pass through the FRB Flatwork Folder, a highly programmable machine with one, two or four feeding lanes, which automatically performs two to three primary folds and up to three cross folds, as needed. Finally, linens are automatically stacked and returned to operators.
The result is a high-quality finish at high-speed production rates, according to Doro. “Our goal is 150 sheets per hour per person using four lanes,” she said. “We can process 400-750 sheets per hour and 4,200 sheets per shift using our ironing system. The other goal is to minimize wrinkles and we’ve been very pleased with the consistent appearance of our sheets.”
Upgrading other Kalahari Properties
So much so, plans are underway to upgrade the ironing lines at the other Kalahari properties. Right now, they are not equipped to produce that sort of volume, according to Doro. Ever focused on continuous improvement, Kalahari will soon upgrade the laundries in Wisconsin, Ohio and Pennsylvania, using Texas as a model.
In Wisconsin, a GI DRM Single Station Feeder will be added to the existing ironing line, which will improve production and quality, while cutting more than 1,800 labor hours per year over handfeeding. In Pennsylvania, a new ironing system — a DRF 3-Station Auto-Clip Feeder, PC120 2-roll thermal fluid ironer and FRB Folder with side stacker — will allow for triple-sheeting for the first time. And, in Ohio, a new GI DRM Single Station Feeder and PC120 Ironer will work in concert with an FRB Folder for enhanced quality and production, as well as reduced labor hours.
At Kalahari, results and quality matter — even in the laundry, according to Doro. “We have performance metrics we want to meet at all of our properties,” she said. “In Texas, our goal is to achieve 100 PPOH (pounds per operator hour), which we often surpass.”
Doro credits this success to Kalahari’s dedicated laundry associates, a facility equipped for quality and productivity, and the Kalahari-GI partnership focused on continuous improvement.
